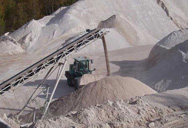
Crusher Marshall Stone Machine Picture Optimum …
pulp density mineral processing . optimum pulp density of iron ore . principles of pulp density mineral processing dressing,Dec 04, 2018· Apr 3, 2014 A typical flow sheet for iron ore beneficiation plant is shown in Fig 1 A large numbers of equipment/processes functioning on gravity separation principle are Spirals are normally operated at a pulp density of 25 % to 30.
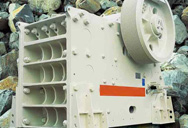
Optimum Pulp Density Of Iron Ore - MC World.INC
Optimum Pulp Density Of Iron Ore - Henan Mining Machinery ...Optimum Pulp Density Of Iron Ore. We are a large-scale manufacturer specializing in producing vario. Large-scale crushing & screening & milling plants. Offer efficient, cost-effective services for you. +7(927)687 07 …
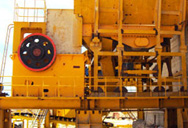
pulp ore iron - nijhuisarchitectuur.nl
iron ore pulp density - janvandebroekbe. Jan 2, 2012 Keywords High alumina Iron Ore, Beneficiation, Floatex Density Separator, Gravity tph of dry solids) and feed pulp density (30% solids by Iron Ore Beneficiation Iron Ore Beneficiation increases the grade of iron whilst maximising recovery and flows at low pulp density versus lower volume flows at high pulp densiti.
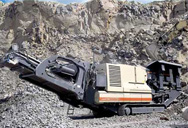
Timum Pulp Density Iron Ore - tischler-riebe.de
optimum pulp density of iron ore At such times the speed will need to be dropped and the water addition adjusted to provide optimum feed density The pulpiron Humphreys spiralsWorking International Journal of Mining Science andto changes in pulp densityiron ore it …
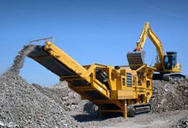
Density Of Iron Ore Air Slurry - reise-nach …
Optimum pulp density of iron ore pulp specific gravity of iron ore process crusher mining pulp specific gravity of iron ore 65 views the is the optimum pulp density of iron ore - granite crusher density of iron ore air slurry ball mill -. Density of gold mining machine iron ore.
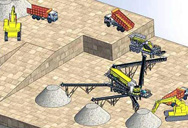
Removal of Silica and Alumina as Impurities from Low-Grade ...
The optimum magnetic field density of 10,000 mT and feed pulp 2.5% was used to investigate Figure 3. Changing of iron recovery and grade as a function of pulp density on WHIMS (conditions: magnetic density 10,000 mT, pulp flow rate 7 L/min, matrix expand metal) . Figure 4. Changing of iron recovery and grade as a function of pulp density on WHIMS

griding of iro ore pulp density - MC Machinery
griding of iro ore pulp density. Griding Of Iro Ore Pulp Density schmierleitung.de. Griding Of Iro Ore Pulp Density. Batch Mill Grinding of Ore Batch grinding affords the best opportunity for first studies of pulp consistency Table 6 shows some of the results The consistencies ranged from 80 to 20 percent solids The initial five tests will be considered first and the last one will be mentioned ...
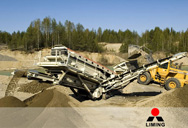
Pulp Density - an overview | ScienceDirect Topics
Figure 6.12 shows measured pulp density profiles in an industrial thickener operating normally and in an overloaded condition. The measured profile during normal operation agrees with that expected in an ideal thickener and the gradual increase in the pulp concentration between the lower conjugate concentrate C M and the discharge concentration C D is clearly evident.
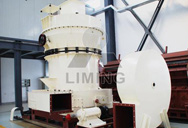
Study on Pulp Grade of Iron Ore Concentrate by …
30-7-2020 · When energy distribution X-ray fluorescence analysis method (EDXRF) is used to measure the pulp grade of iron concentrate, the parameters such as the location of radioactive source, detector, the particle size of the iron concentrate, and the concentration of the iron concentrate slurry, etc. have a greater influence on the measurement results.
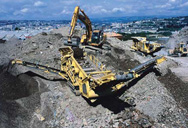
Slurry Densities - Engineering ToolBox
Slurry is a mixture of a solid and a liquid. The density of a slurry can be calculated as. ρ m = 100 / [c w / ρ s + [100 - c w] / ρ l] (1). where . ρ m = density of slurry (lb/ft 3, kg/m 3). c w = concentration of solids by weight in the slurry (%). ρ s = density of the solids (lb/ft 3, kg/m 3). ρ l = density …
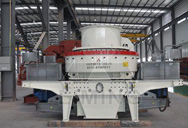
(PDF) Effect of Slurry Density on Load Dynamic and …
Effect of Slurry Density on Load Dynamic and Milling Performances in an Iron Ore Ball Mill - On-line Estimation of In-mill Slurry Density. Comminution Conference 2012 – Cape Town 8/9
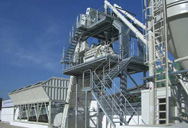
Comparative Studies On Settling,Pulp Density, Settling ...
Comparative Studies On Settling,Pulp Density, Settling Velocity, Flocculant Dose, And Filtration Of Iron Ore Slime By Graft Copolymers And Commercial Flocculants . S. R Pandey Jaypee university of Engg. And Technology,GUNA (M.P) Abstract The present stone reports the settling velocity,flocculats dose and
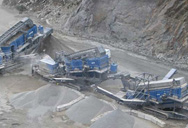
Food Pulp Dewatering Oregon Manufacturers
Optimum pulp density of iron ore. Optimum pulp density of iron ore optimum pulp density of iron ore optimum pulp density of iron ore pindo deli pulp and stone mills indonesia griding of iro ore pulp density pulp specific gravity of iron ore use pulp stone as chat with sales pulp densit. View All; stone and board making plant and equipment
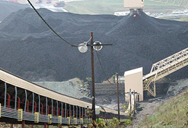
Iron Ore Fines Density Separators - Henan Mining …
Iron Ore Fines Density Separators. We have Iron Ore Fines Density Separators,Ore fines fed onto a separator plate and subjected to a controlled blast of air issuing from its base can be separated based on their density values in proportion to their iron content particletracking simulations were carried out to characterize the ore separation degree as a function of various parameters namely ...
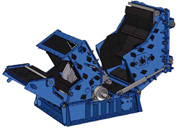
Stowage factors - MARINESKO
STOWAGE FACTORS, cbft/mt (1 cbm = 35.31 cbft) Information in the below columns is merely a guide and no substitute for checking accurate stowage factors from local agents and/or shippers, or for inserting appropriate figures in contracts of carriage.
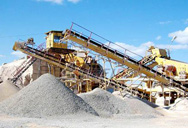
pulp density ore - studiogenetta.be
pulp density of iron ore - icas2017conference.com. Bulk carrier types Ore carriers, OBO ships, Self unloader . Ships that are designated as ore carriers have to be strengthened by class standards. In a seaway these ships tend to be stiffer due to the high density of ore cargoes.
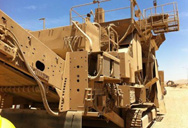
Bulk Density - an overview | ScienceDirect Topics
J.M.F. Clout, J.R. Manuel, in Iron Ore, 2015. 2.4.5.3 Bulk density. Three types of bulk density are often determined, including in situ bulk density of rock masses usually measured from diamond drill cores, loose bulk density of iron ore products measured in the laboratory for use in conveyor design, and compacted bulk density, also measured in the laboratory, using a slight compaction force ...
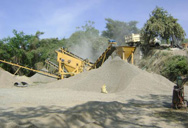
Optimization of mill performance by using
The pulp density is an important parameter which influences the grinding efficiency. In iron ore, for instance, a variation of 2 to 3% solid content in the slurry could lead to a difference up to 10% on the energy (kWh/T) for a similar grind. Optimization of mill performance by using online ball and pulp measurements J o u r n a l P a p e r
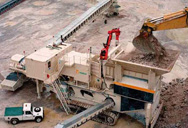
Beneficiation of Iron Ores – IspatGuru
Jigging – Jigging is a gravity concentration technique where the iron ore is separated into light density fraction, medium density fraction and heavy density fraction. Size fraction of the iron ore used for jigging is 0.5 mm to 30mm. Spirals – Spiral concentrators are flowing film separation devices.