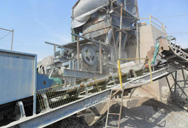
Factors Affecting Ball Mill Grinding Efficiency
The following are factors that have been investigated and applied in conventional ball milling in order to maximize grinding efficiency: a) Mill Geometry and Speed – Bond (1954) observed grinding efficiency to be a function of ball mill diameter, and established empirical relationships for recommended media size and mill speed that take this factor into account. As well, mills …
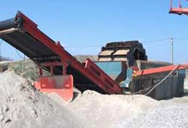
efficiency calculation of a grinding mill thesis
The first two Grinding Efficiency Measurement examples are given to show how to calculate Wio and Wioc for single stage ball mills. Figure 1. The first example is a comparison of two parallel mills from a daily operating report. Mill size 5.03m x 6.1m (16.5′ x 20′ with a ID of 16′). get price
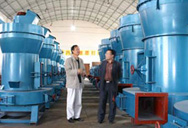
Ball Mills - an overview | ScienceDirect Topics
For many decades the two-compartment ball mill in closed circuit with a high-efficiency separator has been the mill of choice. In the last decade vertical mills have taken an increasing share of the cement milling market, not least because the specific power consumption of vertical mills is about 30% less than that of ball mills and for finely ground cement less still.
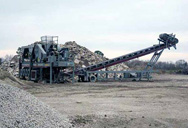
MODULE #5: FUNCTIONAL PERFOMANCE OF BALL MILLING
Ball mill = coarse particles (in the plant ball mill) grinding efficiency Ore grindability (in the lab ball mill) The units of "ball mill grinding efficiency" will be covered in detail in the first part of the module. Alternatively, we can say that: Specific grinding rate = Ball mill x Ore grindability
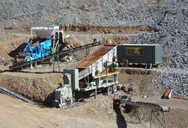
CALCULATION OF BALL MILL GRINDING …
8-3-2013 · calculation of ball mill grinding efficiency. dear experts . please tell me how to calculate the grinding efficiency of a closed ckt & open ckt ball mill. in literatures it is written that the grinding efficiency of ball mill is very less [less than 10%]. please expalin in a n excel sheet to calcualte the same. thanks. sidhant. reply
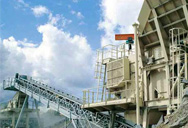
Mill (grinding) - Wikipedia
A mill is a device that breaks solid materials into smaller pieces by grinding, crushing, or cutting. Such comminution is an important unit operation in many processes.There are many different types of mills and many types of materials processed in them. Historically mills were powered by hand (e.g., via a hand crank), working animal (e.g., horse mill), wind or water ().
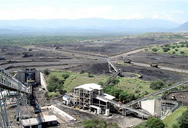
The operating principle of the ball mill - Primo Pizza
The disadvantages of ball mills include their considerable metal consumption and deterioration grinding media, as well as a lot of noise. Most of the energy useless lost during ball mill operation, leading to low it efficiency. But even a significant specific energy consumption for grinding material compensates beneficial effect by using mill.
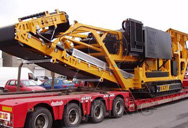
Cement mill - Wikipedia
Closed-circuit systems. The efficiency of the early stages of grinding in a ball mill is much greater than that for formation of ultra-fine particles, so ball mills operate most efficiently by making a coarse product, the fine fractions of this then being separated, and the coarse part being returned to the mill inlet.
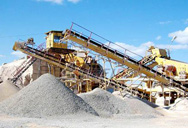
Optimization of mill performance by using
Optimization of mill performance by using online ball and pulp measurements by B. Clermont* and B. de Haas* Synopsis Ball mills are usually the largest consumers of energy within a mineral concentrator. Comminution is responsible for 50% of the total mineral processing cost. In today’s global markets, expanding mining groups are trying
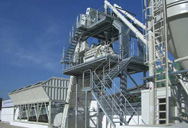
Ball Mill Design/Power Calculation
The basic parameters used in ball mill design (power calculations), rod mill or any tumbling mill sizing are; material to be ground, characteristics, Bond Work Index, bulk density, specific density, desired mill tonnage capacity DTPH, operating % solids or pulp density, feed size as F80 and maximum ‘chunk size’, product size as P80 and maximum and finally the type of circuit …
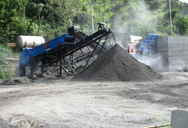
Ball Cement Mill In Operation - vloerverwarming …
Maintenance of ball mill equipment is the main parts of lubrication and maintenance on it. Check the operation status of the ball mill equipment regularly can make the ball mill equipment working years growth. All the lubricating oil input for a month in the ball mill operation should be all released, thorough cleaning, the replacement of the ...
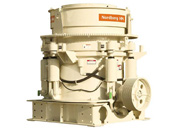
Comminution processes: Basics and application to energy ...
Different possibilities to define energy efficiency: 1. Specific energy of mill compared to new created surface energy → not meaningful, ... Tumbling mill Vibrating mill Planetary ball mill Stirred ball mill Mills with loose grinding media. Overview crusher and mill types
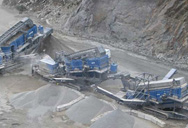
Energy efficiency - IsaMill™ Advantages | Isamill
The large scale of the IsaMill™ makes that efficiency available to mainstream grinding. The high energy efficiency of stirred mills compared to ball mills is well understood. The use of tower mills as an energy efficient alternative to secondary and regrind ball milling became a common inclusion in the latter part of the previous century.
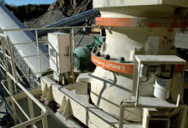
Effect of ball and feed particle size distribution on …
1-6-2018 · Effect of ball and feed particle size distribution on the milling efficiency of a ball mill: An attainable region approach. Author links open ... the measured sample together with the specified size of grinding media were then fed into the mill whose operating conditions are specified in Table 2. The feed material was ...
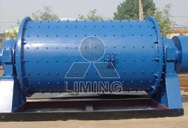
Ball Mill: Operating principles, components, Uses ...
Several types of ball mills exist. They differ to an extent in their operating principle. They also differ in their maximum capacity of the milling vessel, ranging from 0.010 liters for planetary ball mills, mixer mills, or vibration ball mills to several 100 liters for horizontal rolling ball mills.
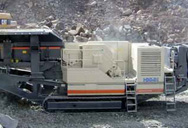
To increase productivity of ball mill - Henan …
Ball Mill DesignPower Calculation. The basic parameters used in ball mill design power calculations rod mill or any tumbling mill sizing are material to be ground characteristics Bond Work Index bulk density specific density desired mill tonnage capacity DTPH operating solids or pulp density feed size as F80 and maximum chunk sizeproduct size as P80 and maximum and …
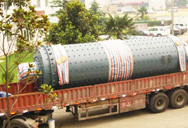
improved grinding media for ball mills industrial ...
Factors Affecting Ball Mill Grinding Efficiency. 29 · The following are factors that have been investigated and applied in conventional ball milling in order to maximize grinding efficiency: a) Mill Geometry and Speed – Bond (1954) observed grinding efficiency to be a function of ball mill diameter, and established empirical relationships for recommended media size and mill speed …
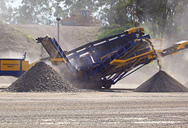
Energy Saving High Efficiency Ball Mill Price
Ball mill ,ball mill for sale,ball mill grinding machinery ,ball mill ,ball mill, ball mill direct from henan zhengzhou,ball mill, ball mill direct from zhengzhou jiangtai,ball mills in hyderabad, telangana ,china ball mill manufacturer, flotation cell, crusher ,china cr8001000 milling machine impact mill,china gzm series conical ball mill ,