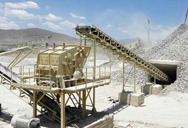
Optimization of continuous ball mills used for …
10-12-2004 · This mill at the Polysius R&D centre is used for grindability testing mainly. Seventeen different ball gradings were tested. The lab-mill (∅ 0.75×0.45 m, ball charge filling ratio 10%, relative mill speed 0.88) were fed with clinker meal with a Blaine surface area of 2700 cm 2 /g.
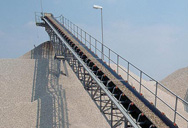
Optimisation of the ball charge in mills for cement ...
Optimisation of the ball charge in mills for cement grinding Article in Cement International 7(6):42-47 · November 2009 with 43 Reads How we measure reads
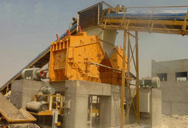
Optimization of mill performance by using
Stresses, generated in the ball charge, increase, which may result in spalling of balls and blocking the grate discharge. Optimization of mill performance by using online ball and pulp measurements by B. Clermont* and B. de Haas* Synopsis Ball mills are usually the largest consumers of energy within a mineral concentrator.
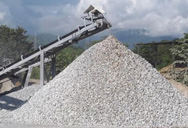
cement mill optimization - ilbuonodellacucina.it
Cement Grinding Cement Plant Optimization,Closed circuit ball mill with two compartments for coarse and fine grinding are generally found in cement plants for cement grinding Compartments filled with grinding media are divided by a double diaphragm with flow control to utilize maximum mill length for effective grinding Grinding media contain balls of different sizes in designed
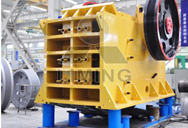
Ball mill understanding & optimisation | Mill …
Filling degree Chamber length Mill diameter Liner design and condition Mill speed. Ball charge (filling degree & composition) Liner design Intermediate diaphragm settings Mill ventilation 34. HGRS. Tikaria_Mill Workshop. SEPT-07 Grinding Media. 4,4 [t/m3] 4,6 [t/m3] 4,7 [t/m3] Bulk weight of a grinding media charge in a two chamber mill with ...
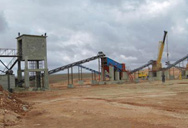
SAG/Ball Mill Optimization | KnowledgeScape
SAG/Ball Mill Optimization. Home | Plantwide Solutions | SAG/Ball | Flotation | Crush & Convey | Thickener | Froth Camera Systems | Conveyor Image Analysis. Better efficiency, starts with better grinding. You’ve already gone through the work to bring the ore to the mill, now it’s time to recover as much precious metal as possible.
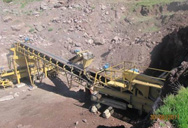
EFFECTS OF GRINDING MEDIA SHAPES ON BALL MILL …
SHAPES ON BALL MILL PERFORMANCE ... Comminution is an important process in mineral processing, power plants, cement production and pharmaceutical industries. ... Considering that worn balls in an industrial mill charge constitute about 15 to 40
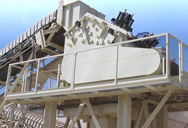
Ball charges calculators - …
- Ball top size (bond formula): calculation of the top size grinding media (balls or cylpebs):-Modification of the Ball Charge: This calculator analyses the granulometry of the material inside the mill and proposes a modification of the ball charge in order to improve the mill efficiency:
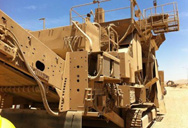
PROCESS DIAGNOSTIC STUDIES FOR CEMENT MILL …
The mill is designed to handle a total ball charge of 324.5 t at 100% loading with a percentage filling of 29.5% in both the chambers. Both the chambers of the cement mill were charged with 80% of the designed charge,
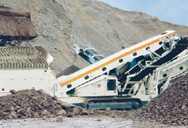
Optimization of continuous ball mills used for …
Optimization of continuous ball mills used for finish-grinding of cement by varying the L/D ratio, ball charge filling ratio, ... The number of stresses can be characterised by the average retention time of the ground material inside the mill if the ball charge grading remains unchanged.
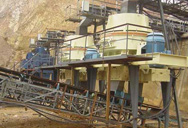
Cement Grinding Optimization - LinkedIn SlideShare
31-7-2014 · Cement Grinding Optimization 1. CEMENT ... model for tumbling mills (Morrell, 1998). Bond method The established technique for determining power requirements for ball mills is the Bond method (Bond, ... the ball charge size distribution in the first compartment needs to …
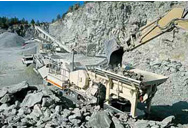
Abstract On Cement Ball Mill Optimization
Abstract On Cement Ball Mill Optimization. Abstract On Cement Ball Mill Optimization; Cement grinding optimisation Request PDF. The energy efficiency of ball mills for use in finish grinding is relatively low, consuming up to 30-42 kWh/ton clinker depending on the fineness of the cement (Cembureau, 1997;Marchal, 1997).
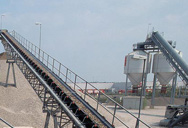
Cement Ball Mill Grinding Media Density
Cement Ball Mill Grinding Media Density. Effects of grinding media shapes on ball mill . comminution is an important process in mineral processing power plants cement production and pharmaceutical industries it is costly and an inefficient process in terms of energy requirements and steel consumption related to grinding media and liners spherical grinding media are predominantly used in final ...
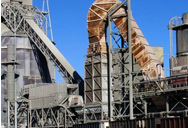
Optimization of continuous ball mills used for …
Download Citation | Optimization of continuous ball mills used for finish-grinding of cement by varying the L/D ratio, ball charge filling ratio, ball size and residence time | During the last ...
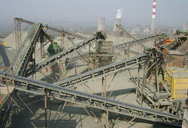
CONTROL, OPTIMIZATION AND MONITORING OF PORTLAND …
CONTROL, OPTIMIZATION AND MONITORING OF PORTLAND CEMENT (PC 42.5) QUALITY AT THE BALL MILL A Thesis Submitted to the Graduate School of Engineering and Sciences of zmir Institute of Technology in Partial Fulfillment of the Requirements for the Degree of MASTER OF SCIENCE in stone Engineering by Hakan AVAR January 2006 ZMR
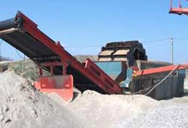
European Cement Research European Cement Research Academy
6.1 Stirred media mills for cement production 48 6.2 Ecopulser (Krause, Germany) ... These can be used for optimization of existing grinding plants (e.g. ball charge grading in ball mills). This can short-term improve troughput, efficiency, reliability, ...