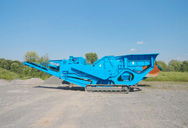
validation process of ball mill - …
validation process of ball mill. Home; ... Ball mills are used primary for single stage fine grinding, regrinding, and as the second stage in two ...
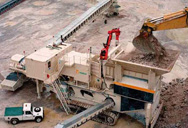
Validation Process Of Ball Mill - 5-tage-5-fluesse.de
Validation Process Of Ball Mill. Ball mills scale up well and in fact improve in performed with increasing size. ball mills are available in sizes from laboratory scale also called milling jars of 0.1 usg to large 5,000 gallon mills. ball mills are available in various contact materials to accommodate contamination and wear requirements.
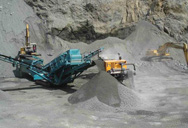
validation process of ball mill – Grinding Mill China
ball mill process validation Description : X53149-k.ray Poster-37×381 – Sigma-Aldrich broad terms, it states that the process validation program for a pow- dered » Learn More. Guidance for Industry. 2 In the guidance for industry, process with the new equipment is validated, the mill …
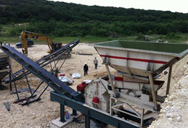
Ball Mill: Operating principles, components, Uses ...
A ball mill also known as pebble mill or tumbling mill is a milling machine that consists of a hallow cylinder containing balls; mounted on a metallic frame such that it can be rotated along its longitudinal axis. The balls which could be of different diameter occupy 30 – 50 % of the mill volume and its size depends on the feed and mill size.
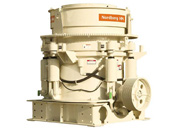
Ball mill - Wikipedia
A ball mill is a type of grinder used to grind, blend and sometimes for mixing of materials for use in mineral dressing processes, paints, pyrotechnics, ceramics, and selective laser sintering.It works on the principle of impact and attrition: size reduction is done by impact as the balls drop from near the top of the shell. A ball mill consists of a hollow cylindrical
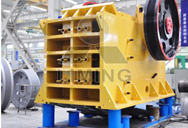
3D Animation Demo & working site of Ball Mill - …
13-11-2014 · The Mining Process at Copper Mountain Mine - Duration: 7:13. CopperMountainMining Recommended for you. ... Ball mill, Grinding machine, Wet ball mill, Dry ball mill, Milling machine ...
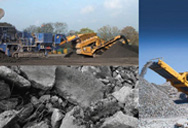
Ball Mills - an overview | ScienceDirect Topics
Ball mills could operate dry or even process a water suspension (almost always for ores). Dry, it is fed through a chute or a screw through the unit’s opening. In a wet path, a system of scoops that turn with the mill is used and it plunges into a stationary tank.

(PDF) DESIGN AND FABRICATION OF MINI BALL …
This project is to design and fabricate the mini ball mill that can grind the solid state of various type of materials into nano-powder. The cylindrical jar is used as a mill that would rotate the ...
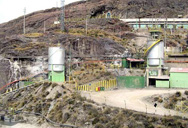
Process Validation on CNC Lathe and Milling …
8-5-2014 · With regard to medical devices and components, I am very much familiar with Process Validation on Injection Molding processes. Typically Time, Temperature and Pressure are the main factors adjusted for Par High and Par Low runs to optimize nominal parameters. I now find myself in uncharted territory; Lathe and milling operations.
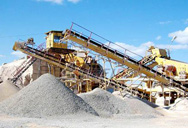
Optimization of mill performance by using
Optimization of mill performance by using online ball and pulp measurements by B. Clermont* and B. de Haas* Synopsis Ball mills are usually the largest consumers of energy within a mineral concentrator. Comminution is responsible for 50% of the total mineral processing cost. In today’s global markets, expanding mining groups are trying
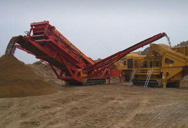
Ball Mill Design/Power Calculation - LinkedIn
12-12-2016 · If P is less than 80% passing 70 microns, power consumption will be. Ball Mill Power Calculation Example. A wet grinding ball mill in closed circuit is to be fed 100 TPH of a material with a work ...
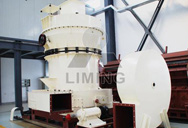
How to Make a Ball Mill: 12 Steps (with Pictures) - …
29-3-2019 · Making a ball mill is a relatively simple process, but there are quite a few materials needed. A lot of the supplies can be recycled from other projects and found in junk piles, but some may need to be purchased. Once you have the following materials, you can start building ...
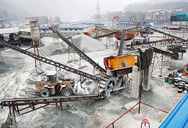
Validation of a closed circuit ball mill model
1-1-2013 · Minerals processing engineers and grinding experts agree that classification efficiency and circulating load both have a major effect on the efficiency of closed circuit ball mills. However, the effect of each is difficult to quantify in practice as these two parameters are usually interrelated. Experimental work was undertaken by liming Process Technology and …
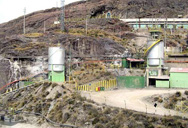
A new model-based approach for power plant …
1-4-2014 · Tube-ball mill is another dominant type of coal mill apart from Vertical Spindle mill in industry. Compared with the Vertical Spindle mills, Tube-ball mills have a much higher grinding capacity. However, there are fewer literatures found in studying Tube-ball mill operation compared with the Vertical Spindle mill.
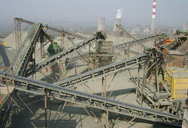
AMIT 135: Lesson 7 Ball Mills & Circuits – Mining …
Describe the components of ball mill. Explain their understanding of ball mill operation. Explain the role of critical speed and power draw in design and process control. Recognize important considerations in ball mill selection. Reading & Lecture. In ball mills, steel balls or hard pebbles to break particle based on impact and attrition.
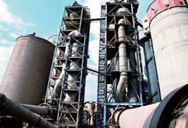
Ball Milling | Material Milling, Jet Milling | AVEKA
Ball milling is a size reduction technique that uses media in a rotating cylindrical chamber to mill materials to a fine powder. As the chamber rotates, the media is lifted up on the rising side and then cascades down from near the top of the chamber.
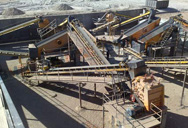
EFFECT OF BALL SIZE DISTRIBUTION ON MILLING PARAMETERS
Lastly, I would like to thank the Centre of Material and Process Synthesis of the University ... 5.3.2 Validation of ball mixture model 67 5.3.3 Significance of findings 68 5.4 Summary 70 ... 2.1 Breakage mechanisms in a ball mill 22
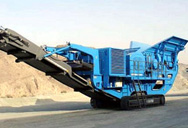
Nano Ball Milling - SlideShare
15-12-2012 · Ball milling is a method of production of nano materials. This process is used in producing metallic and ceramic nano materials. These mills are equipped with grinding media composed of wolfram carbide or steel. Ball mills rotate around a horizontal axis ,partially filled with the material to be ground plus the grinding medium. 6.

DEM modeling of ball mills with experimental …
25-7-2016 · Dong H, Moys MH (2002) Assessment of discrete element method for one ball bouncing in a grinding mill. Int J Miner Process 65(3–4):213–226. doi: 10.1016/S0301-7516(01)00083-7 CrossRef Google Scholar
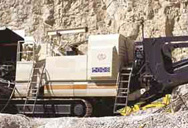
How Ball Mills Work (Engineering and Mining) - …
20-6-2019 · How Ball Mills Work The following process description is based upon a ball mill used in the hard rock mining industry for liberating minerals from ore, but the operating principle for ball mills ...