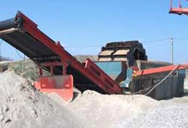
Operation Guide for Vertical Roller Mill in Cement Plant ...
Vertical Roller Mill Operation in Cement Plant The vertical roller mill (VRM) is a type of grinding machine for raw material processing and cement grinding in the cement manufacturing process.

operation of vertical raw mill cement industry
Vertical Raw Mill China Manufacturer, Vertical RollerVertical raw mill company. 17/2/2016· In this training module, well cover the operation of a vertical roller mill This mill is commonly used in the cement industry in order to grind raw feed Well describe the general arrangement.Vertical Roller Mill In Cement IndustryVertical Roller Mill In Cement Industry Vertical roller mills ...
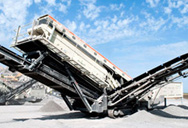
The cement kiln
Most new cement plant is of this type. The principle is similar to that of the dry process preheater system but with the major addition of another burner, or precalciner. With the additional heat, about 85%-95% of the meal is decarbonated before it enters the kiln. Basic principle of a …
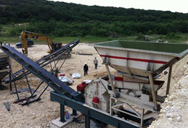
Clinkerization - Cement Plant Optimization
The conversion taking place in kiln system as raw meal is heated gradually to clinkerization temperature (1450 0 C) as shown below in table 1. Kiln system has seen a sea of development since 1950s to till date, from vertical shaft kilns to modern pre-calciner kiln. Capacity has increased from as low as 50 tpd to as high as 12000 tpd from kiln.
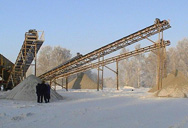
vertical raw meal mill technology book pdf
modern vertical roller grinding mills along with tube mills both for raw meal as well as coal. Cement grinding is achieved exclusively by tube mills/horizontal ball mills. The final products of the plant include PPC, OPC, PSG and other special cements. The major markets are Tamil Nadu, Kerala, Karnataka, Andhra Pradesh, Pudducherry etc. 2.
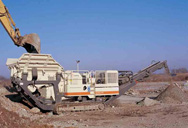
Cement grinding Vertical roller mills versus ball mills
cement ground in OK mills similar to those for cement ground in ball mills (BM), as shown in Figure 6. Figure 6: B It should be noted, however, that operation to achieve a wide particle size distribution (low n-value) has a cost. The measures taken to achieve a low inclination of the PSD
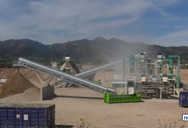
mill operation cement plant - boerenlandwandelen.nl
Vertical Roller Mills. Years of experience helping the cement and power plant industries achieve easy operation and maintenance, energy efficiency and cost savings underpin our expertly-designed vertical roller mill (VRM) product range Whether grinding raw coal, clinker, cement and/or slag, we have a VRM solution to suit your grinding needs...
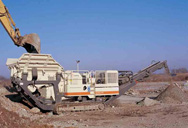
cement-plant-operation-handbook - LinkedIn SlideShare
May 27, 2016 · cement-plant-operation-handbook 1. TERNATIONAL • Revieww July 1998 Philip A Alsop CEMENT I_ A NI 1- OPERATIONS HANDBOOK 1 Second Edition The concise guide to cement manufacture -I- FA E. • 2. CEMENT PLANT OPERATIONS HANDBOOK For Dry Process Plants Philip A Alsop, PhD Second Edition July 1998 Tradeship Publications Ltd 3.
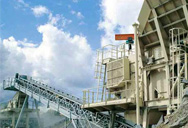
Vertical Cement Mill Stepwise Process Operation Crusher
Vertical Cement Mill Stepwise Process Operation Crusher. Portable crusher plant is a kind of novel rock crushing equipment greatly expand the coarse crushing operation concept lum ultrafine vertical roller mill vertical roller mill is a kind of equipment used for raw cement cement clinker slag and clinker grinding processing has the characteristics of simple structure low cost of manufacture

VRM to Crown operations - cemnet.com
11 hours ago · When Crown Cement identified the need to increase the cement capacity of its plant in Bangladesh it opted for vertical roller mill (VRM) technology from Loesche. With a range of VRM benefits, total grinding capacity has increased to 11,000tpd and has offered more product versality with local operating conditions in mind.
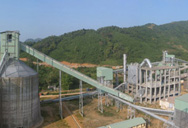
meal grinding raw - themadreven.nl
Raw Material Drying-Grinding - Cement Plant Optimization. Grinding Operation Objectives and KPIs: Highly energy intensive unit operation of size reduction in cement industry is intended to provide a homogeneous, dry (0.5% moisture) and super fine (10-20% residue on 90-micron sieve) raw meal powder for clinkerization process in kiln (Dry Process).). Grinding operation is monitored for follow
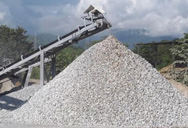
Vertical roller mill - Wikipedia
Operation. Material grinding process motor through reducer rotating drive disc, the material falls from the mill under the central entrance and exit, under the action of centrifugal force to the disc edge by the roller to move and the crushing, grinding out lap after the material was speed up the flow to and vertical mill with one of the separator, after the meal by the separator back to the ...
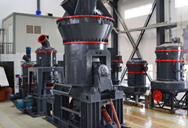
Operational parameters affecting the vertical roller mill ...
Vertical roller mills (VRM) have found applications mostly in cement grinding operations where they were used in raw meal and finish grinding stages and in power plants for coal grinding. The mill combines crushing, grinding, classification and if necessary drying operations in one unit and enables to decrease number of equipment in grinding ...
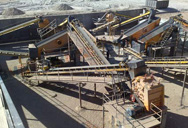
Vertical Roller Mills - FLSmidth
Within the cement industry, vertical roller mills are becoming more important as more cement producers look to increase their use of clinker substitute materials instead of importing clinker to meet localised rises in cement demand. The advantages of the vertical roller mill include a high level of grinding efficiency combined with reduced energy consumption.
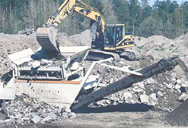
cement plant optimization
Mission #1: Knowledge and skill development of cement plant professionals to make them self sufficient to identify optimization opportunities in cement plant operation. Mission #2: Visualization of present performance level and road map to achieve potential performance through process and energy audit.
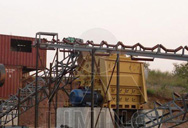
Grinding technology and mill operations | FLSmidth
Ball mills and vertical roller mills are used for many grinding applications in cement production: raw meal grinding, coal and stone coke, and finish cement grinding. Improving the competences of the team plays a key role in the optimal utilisation of the grinding installation in your cement plant.
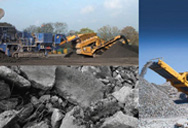
Rawmill - Wikipedia
Note: LoI 950 is the Loss on ignition at 950 °C, and represents (approximately) the components lost during kiln processing. It consists mainly of CO 2 from carbonates, H 2 O from clay hydrates, and organic carbon.. Using these materials, typical rawmixes could be composed: Mix 1: General-purpose cement: 88.0% gray limestone, 8.9% clay, 2.2% sand and 0.9% millscale.
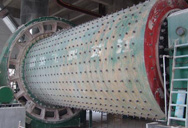
): Automation solutions for the Cement Industry.
The Cement Industry is moving in a constant area of tension between optimum quality, lower costs and shorter time-to-market. Whether you are a plant operator, system integrator or plant and machine constructor: the solution to this problem is Totally Integrated Automation. Advantages for plant operation
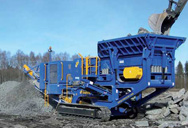
Cyclone Preheater in Cement Plant | Suspension Cement ...
Cyclone preheaters are also called suspension preheaters. In the new dry process of cement manufacturing, the raw meal must be preheated in the preheater before entering the rotary kiln for calcining.The quality of the preheater in a cement plant directly affects the stability of calcining temperature and cement clinker quality in the kiln.